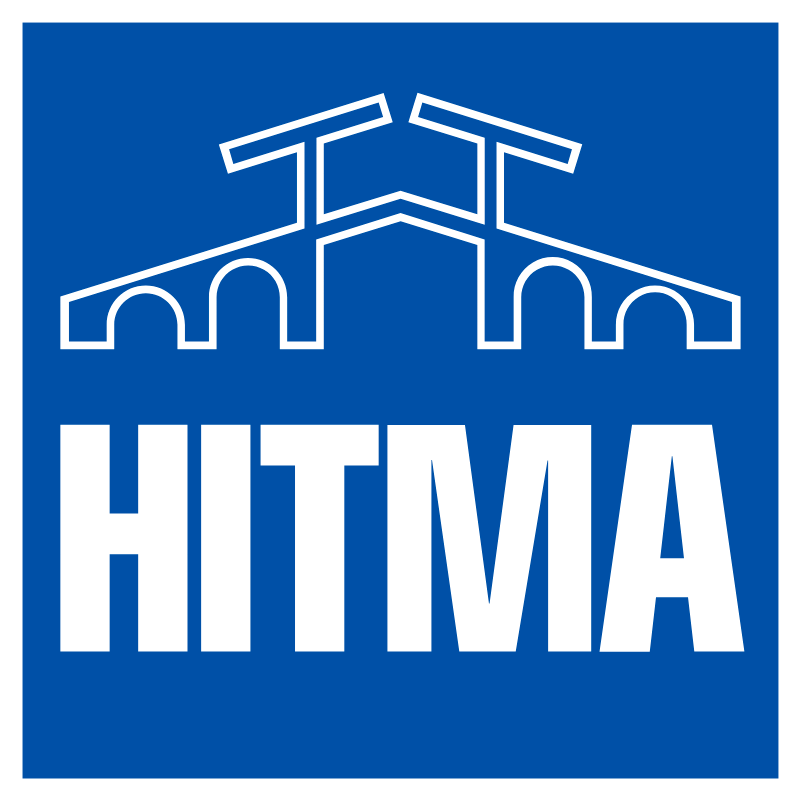
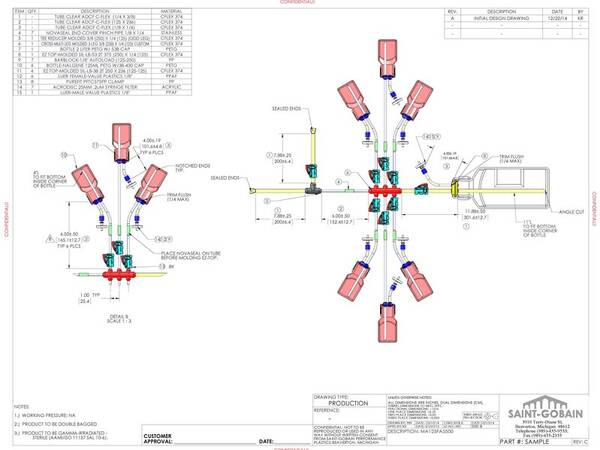
Het is grappig om te zien hoe omvangrijke single-use projecten soms ‘bij toeval’ tot stand komen. Mooi voorbeeld is een project voor een farmaceutische klant waar we een presentatie gaven over één van onze single-use productlijnen. Toevallig kwam ter sprake dat ze in hun proces lekkageproblemen hadden. We legden uit dat dit verholpen kon worden door op alle locaties in het proces waar ze tyraps gebruikten, Barblocks® te plaatsen.
Lekvrije koppelingen
Barblocks zijn veilige montageringen voor veeleisende koppelingstoepassingen. Ze zijn snel en gemakkelijk te assembleren en vervangen lekgevoelige kabelbinders en traditionele klemmen. Barblocks zijn compatibel met alle soorten flexibele tubing.
De tip over de Barblocks heeft uiteindelijk geleid tot een volledige redesign van hun systeem. Aan de assemblies in hun proces kon je zien dat ze geen ervaring hadden met molded products. Er werden veel reducers toegepast. Dat is jammer, want elk verloopstuk vergroot de kans op lekkage.
Minder kans op lekkage en contaminatie
Na dit met de procesoperator en productiemanager te hebben besproken, was men het met ons eens dat het beter zou zijn zoveel mogelijk over te gaan op closed loop overmolded producten. Dit zou het aantal lekkagepunten terugbrengen. Het bedrijf produceert een steriel product en het is voor deze farmaceut van groot belang dat ze de kans op contaminatie zoveel mogelijk kunnen verkleinen. Bijkomend voordeel is dat wij ze een oplossing kunnen bieden waarbij ze minder soorten tubing gaan toepassen. Hierdoor hoeven er ook minder losse onderdelen gevalideerd te worden.
Audit bij de fabriek
De klant werd enthousiast. Ze zagen de voordelen voor hun proces, maar wilden graag eerst twee productielocaties van Saint-Gobain (SGPPL) in de VS bezoeken. Ze wilden met eigen ogen zien dat de mooie oplossing die wij ze beloofden ook daadwerkelijk zo uitgevoerd kon worden.
Dus vertrokken ik samen met de procesoperator, QA-manager en productiemanager van de klant voor een audit naar de SGPPL-fabrieken in St. Paul (hoofdstad van de Amerikaanse staat Minnesota) en in Beaverton in het noordwesten van Michigan, op slechts twee uur ten noorden van Detroit. Deze ISO 9001-gecertificeerde faciliteiten produceren single-use producten voor de farmaceutische markt van o.a. Pure-Fit® , Sani-Tech® en BioSimplex®.
Snel schakelen via webinar
Na het bezoek aan de Saint-Gobain-fabrieken was de klant ervan overtuigd dat wij de juiste partij voor hen zijn. We hadden hun probleem onderkend en boden nu een manier om het op te lossen. En nog belangrijker: we konden dit op korte termijn voor ze realiseren. We organiseerden een webinar waaraan via een live-verbinding zowel de specialisten van het farmaceutische bedrijf en van SGPPL als van HITMA UltraPure deelnamen. De klant gaf zijn wensen aan en de techneuten van SGPPL in Amerika verwerkten dit à la minute in hun ontwerpprogramma. Zo werkte de klant zelf mee aan de redesign en waren de verbeteringen van hun systeem direct op het scherm voor iedereen zichtbaar.
Binnen twee online sessies was het finale ontwerp een feit. Normaal kan zo’n proces wel 3 tot 6 maanden in beslag nemen. Na definitief akkoord van de klant kan de productie van de assemblies meteen beginnen. De klant was blij verrast over de snelheid.
Supply chain controleerbaar
Dit project levert de klant een single-use systeem op waarin zo min mogelijk verschillende materialen zijn opgenomen. Het aantal mogelijke lekkagepunten is hierdoor tot een minimum teruggebracht. De assemblies bestaan nu voornamelijk uit Saint-Gobain producten in plaats van onderdelen van 4 á 5 verschillende leveranciers. Dit maakt de supply chain beter controleerbaar.
Het mooie aan dit project is dat de klant zich realiseert dat hij deze oplossing ook op andere plaatsen in de fabriek kan toepassen om lekkageproblemen op te lossen. Wij helpen ze hier graag bij al dan niet met behulp van een live-verbinding met de specialisten van Saint-Gobain aan de andere kant van de oceaan.