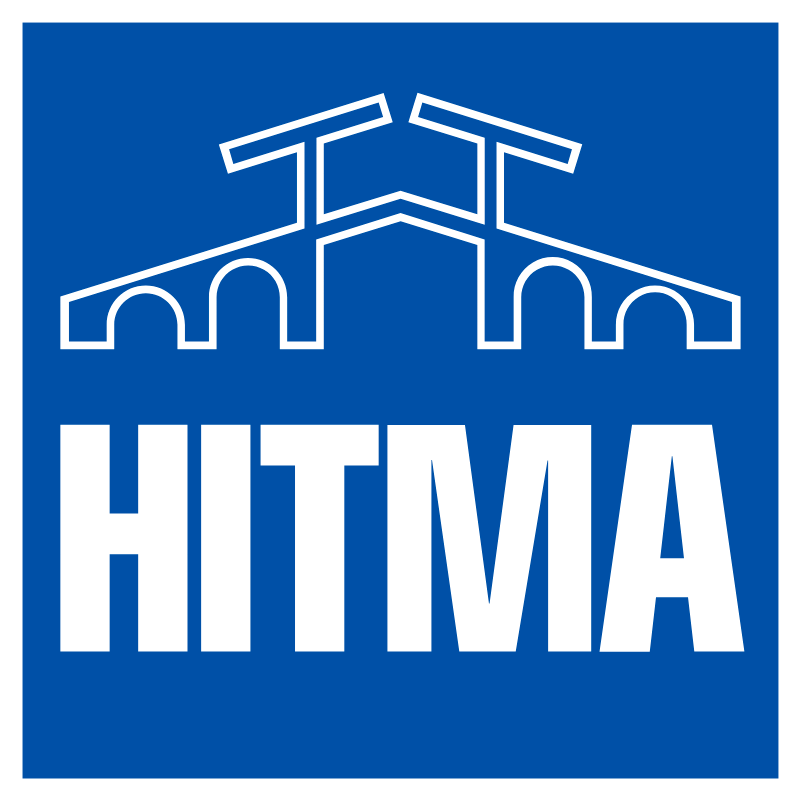
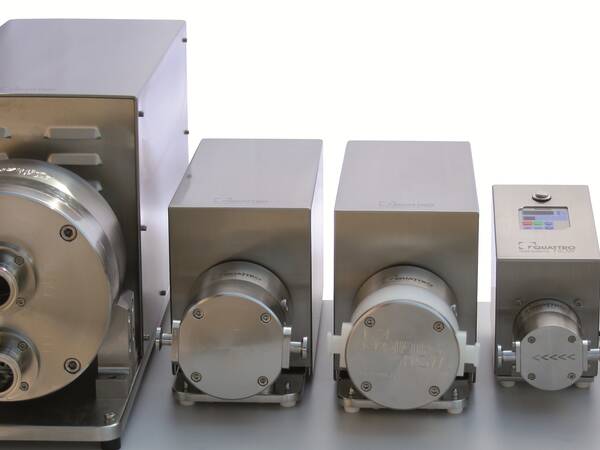
Pumps play an essential role in all parts of a biopharmaceutic process. But how do you decide on the best pump for your process? In this blog, I provide a deep dive into the strengths and weaknesses of different pump technologies and how to choose the best pump for your application.
Pumps throughout the pharmaceutical process
Pumps are used in all different stages of the production of biopharmaceutical products. In upstream processes (USP), cells or microorganisms are cultivated to produce drugs or other biomolecules. Pumps in this process need to ensure gentle handling to maintain cell viability and prevent shear stress. Diaphragm pumps and levitating pumps are often favored for their gentle, pulsation-free operation. With less sensitive drugs or fluids also pumps that induce shear stress or energy influx can be used.
After the production of the biologic compound, it will be purified and concentrated in the downstream processing (DSP). Pumps in DSP should handle high-purity fluids and offer precise control over flow rates to aid in efficient filtration, chromatography, and separation processes. Here, diaphragm pumps are advantageous for their ability to minimize contamination and mechanical impact on sensitive molecules and also not induce pulsation. If pulsation is not a problem as for certain filtration processes than also peristaltic pumps or centrifugal pumps can be used.
In the final stage of fill and finish, aseptic filling of the product into vials or syringes takes place. Minimization of contamination risks is of utmost importance to ensure the highest level of safety of the product, as it will often be administrated to patients. Peristaltic pumps are mostly used in this stage, due to the no drug-product contact principle of the pump, but also peristaltic pumps and diaphragm pumps are used.
The right pump for each process
When selecting the right pump technology for biopharmaceutical processes, there are several crucial factors to consider to ensure optimal integration and performance. The nature of the fluid is paramount: viscosity, corrosiveness, and whether the fluid contains particles can dramatically influence pump choice. Sensitivity to shear and pulsation should also be evaluated, as some biologics, such as live cells and proteins, are very susceptible to damage from mechanical forces. Next to that, operational requirements such as flow rate, pressure demands, and whether the process needs continuous or intermittent flow will further narrow down your choices.
In general, there are four options:
- Peristaltic pumps are particularly favored in processes where hygiene and contamination risks are a concern due to their non-intrusive fluid handling capabilities. They work on a simple principle where a flexible tube is compressed by a set of rollers. As the rollers move, they push the fluid through the flexible tubing in a wave-like motion with a squeeze and release action. This method is called peristalsis, similar to how your gastrointestinal tract moves food. It is therefore eminently safeguarding the fluids purity and integrity.
- Diaphragm pumps are particularly valued for their ability to maintain product integrity in processes where the utmost care is required to handle fluids gently and maintain a sterile environment. These pumps utilize a four-piston diaphragm technology that nicely mimics the human heart's action to deliver gentle, low-shear pumping. This design allows for a smooth, pulsation-free flow which is ideal for handling sensitive biological materials. It can also create its own vacuum like the peristaltic pump, which enables freedom in the placement of your pump in your process. It does not depend on gravity and diminishes the influence of air (bubbles) which are of concern for levitating pumps.
- Centrifugal pumps are mainly used in high throughput applications and are therefore commonly used for pumping large volumes in for instance cooling and irrigation systems, water purification, and other applications. They operate using a rotating impeller to add energy to the fluid, which is then directed outwards to the pump's discharge by centrifugal force. Centrifugal pumps are the workhorses of fluid movement, using rapid rotation to fling liquids through processing paths—ideal for robust, non-sensitive applications.
- Levitating pumps are valued in applications where purity and low maintenance are paramount, though the complexity and costs may limit their use to more specialized environments. These pumps, particularly those employing magnetic levitation technology, are innovative devices that suspend the impeller in a magnetic field, eliminating direct contact with other pump components. This design reduces wear and minimizes contamination risks. By using magnetic fields to suspend their moving parts, almost all physical wear and tear is eliminated and a high purity in fluid handling is ensured. These pumps however cannot create their own vacuum and therefore prone to influencing by air (bubbles). Also, they cannot suck up fluids located below the level of the pump itself.
These are all pumps for mainly big biopharmaceutical production locations. To support research and development departments and other small scale research institutes, Quattroflow has developed a new line of small, microdosing rotary pumps: the QB line.These are lightweight single-use pumps that operate on the positive displacement principle where fixed cavities of liquid are transferred from inlet to outlet around a rotor. They have been designed to simply click in and out of the pump’s motor drive to be replaced with just one click. This eliminates the need for pump recalibration, requalification and maintenance while helping to reduce the risk of cross-contamination. Therefore, the QB pumps are highly suitable for handling shear-sensitive products in cell- and gene therapy applications, as well as small-scale upstream and downstream processes.
In summary, there are many options for pumps and many things to take into account when choosing one. A number of them have been discussed in my webinar. If you want more information or personal advice on which pump is suitable for your process, feel free to contact me.